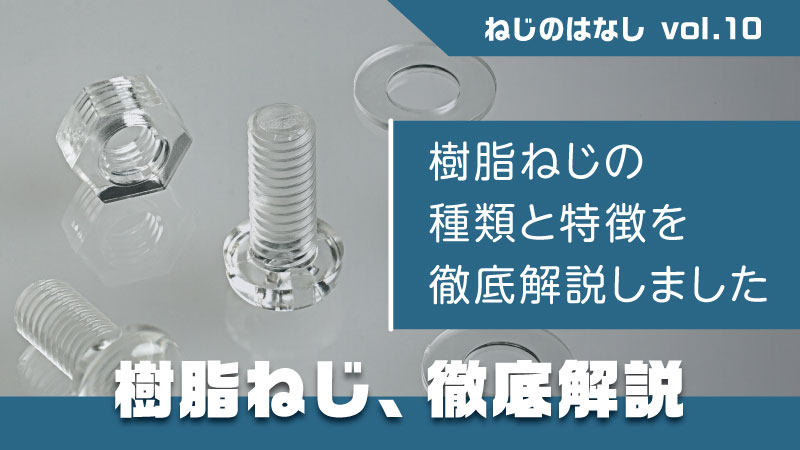
樹脂ねじとは
樹脂ねじは、プラスチック素材で作られたねじであり、軽量でありながら耐腐食性や電気絶縁性に優れているのが特徴です。金属ねじに比べて化学薬品や湿気に対して高い耐性を持つため、電子機器、半導体、化学産業、医療機器などさまざまな分野で活用されています。これにより、金属が使用できない環境や、軽量化が求められる製品での使用が増えています。
近年では、樹脂の素材技術と加工方法が進化し、強度や耐薬品性をさらに向上させた製品が開発されています。業界によっては、製品の最小化、軽量化が求められておりねじについてもその要望を満たす製品として樹脂ねじに対する要望も高まっています。
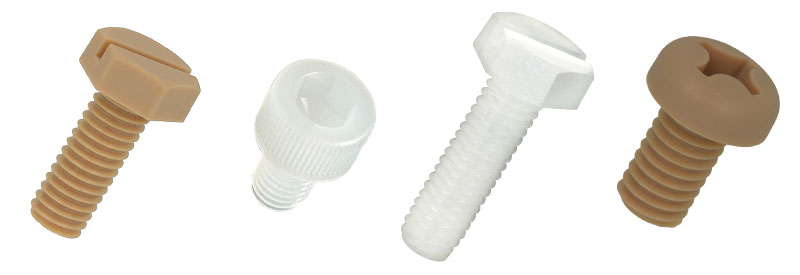
樹脂ねじの基本的な特徴
樹脂ねじの基本的な特徴として、まず挙げられるのはその多様な素材選択肢です。一般的に使用される樹脂素材には、ポリプロピレン(PP)、ポリアセタール(POM)、ナイロン(PA)、およびピーク(PEEK)などがあります。これらの素材は、それぞれ異なる特性を持ち、特定の用途や環境に応じて最適な選択が可能です。例えば、ピークは高い耐薬品性を持ち、半導体の洗浄装置等、薬品を多く使用する環境での使用で最適な材質です。
また、樹脂ねじはリサイクルが容易で環境負荷が低い点も注目されています。再生可能な資源から製造されることも多く、環境への配慮が求められる現代の製造業において、持続可能な選択肢としての地位を確立しています。このように、樹脂ねじはその多様な特性と環境への貢献から、今後も様々な産業においてその需要が拡大していくことが予想されます。
金属ねじとの違い
樹脂ねじの基本的な特徴として、軽量性が挙げられます。金属に比べて圧倒的に軽いため、製品全体の軽量化を実現できます。但し、強度は低い為、構造部品として鉄の代替で考える際には、検討が必要です。樹脂ねじの中で比較的強度が高い材質は、レニー(RENY)です。ポリアミドを主成分にガラス繊維で強化することで高い強度と剛性を実現しています。材料性質として引張強度285MpaとPP等と比較しても約8倍の引張強度があります。但し、鉄SS400の引張強度(450Mpa)と比較すると見劣りします。
樹脂ねじと金属材料の比重比較
素材 | 比重 |
銅 | 8.90 |
ステンレス | 7.93 |
鉄 | 7.87 |
アルミ | 2.7 |
レニー | 1.65 |
ポリカ | 1.2 |
樹脂ねじと鉄材料の引張強度
材料名 | 比重 | ガラス繊維含有率 | 引張強さ (MPa) | 特徴 |
RENY | 1.65 | 50 | 285 | 引張強さ |
PEEK | 1.3 | - | 91 | 耐薬品性 |
PPS | 1.66 | 40 | 198 | 耐熱性 |
PC | 1.2 | - | 62 | 対候性 |
PP | 0.91 | - | 36 | 軽量 |
材料 | 比重 | 引張強さ (MPa) |
SS400 | 7.85 | 450 |
S45C | 7.84 | 828 |
SCM440 | 7.83 | 980 |
SUS304 | 7.93 | 520 |
耐腐食性の観点から考えると、鉄製の金属ねじは表面処理を工夫することで対応できますが、基本的な表面処理は、膜厚を厚くすることで、耐腐食性能を上げる傾向があります。その為、ねじ径の大きさによってはねじの勘合性能を大きく阻害する可能性があります。その点、樹脂ねじは、表面処理を施していない為、安心して使用が可能です。
材質別の特徴
ポリカーボネート(PC)
高透明性と耐衝撃性を兼ね備え、見た目が重要な製品や、衝撃に強いです。
ポリプロピレン(PP)
軽量で耐化学薬品性が高く、特に水や薬品に対する耐性が求められる環境で活躍します。電気絶縁性も良好で、電気機器の組み立てに最適です。
ポリアミド(ナイロン)
耐摩耗性と耐衝撃性に優れ、機械的強度が求められる用途での使用が一般的です。ナイロンねじは、耐熱性が比較的低いため、高温環境では使用を避ける必要があります。
ピーク(PEEK)
高い耐熱性と耐薬品性能を誇り、厳しい環境条件下でも安定した性能を発揮します。化学的安定性にも優れているため、航空宇宙や医療機器などの高精度が求められる分野で使用されます。
PTFE(ポリテトラフルオロエチレン)
高い耐熱性と優れた耐薬品性能、潤滑性を有しています。
PVC(ポリ塩化ビニル)
耐水性、耐酸性、耐アルカリ性、耐溶剤性に優れた材質で価格も安価です。ただし、耐熱性に劣り、燃焼時には塩素ガス等の有害物質が発生する為、作業環境の確保が必要です。(製造可能なメーカーが少ない材質です。特注生産必要な場合はお問合せ下さい。)
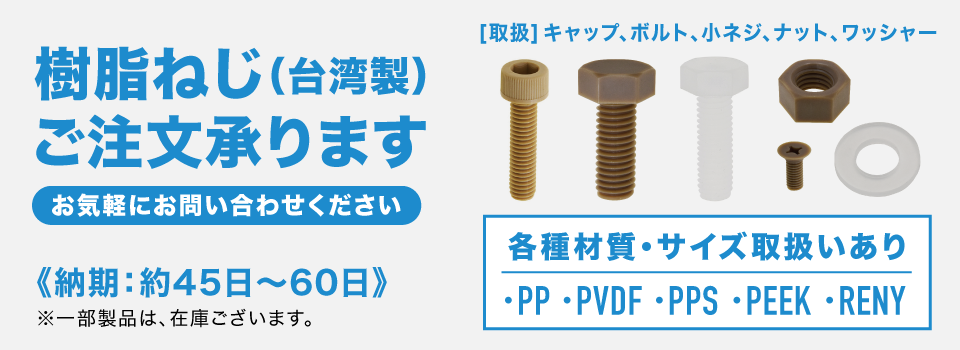
新素材による性能向上
樹脂ねじは、軽量で耐腐食性に優れるため、特に特殊な環境や用途での使用が増えています。近年、樹脂ねじの性能をさらに向上させるために、新素材の導入が進んでいます。これにより、従来の樹脂ねじでは実現できなかった高い強度や耐熱性、そして耐薬品性が実現されています。
例えば、エンジニアリングプラスチックの進化により、ガラス繊維や炭素繊維強化樹脂が開発され、高応力環境下でも形状が安定し、長期的な使用が可能となりました。これにより、自動車や航空機産業における需要が増加しています。また、ナノテクノロジーを活用した樹脂材料の改良により、微細な構造を持つねじが製造できるようになり、電子機器や医療機器への応用が広がっています。
さらに、バイオプラスチックの開発により、環境負荷を低減しつつ高性能を維持する樹脂ねじも登場しています。これらの新素材は、リサイクル可能であり、持続可能な製造プロセスを実現するための重要な要素となっています。
このような新素材の導入によって、従来の樹脂ねじの弱点を克服することができ、より多くの産業分野での採用が進んでいます。樹脂ねじの性能向上は、製品の信頼性を高めるだけでなく、設計の自由度を広げ、新たな応用の可能性を生み出しています。今後も、材料技術の進化に伴い、さらなる性能向上が期待されるでしょう。
強さ・軽さ・耐薬品性を追求した炭素繊維ボルト
炭素繊維ボルトは、従来の金属ボルトとは異なり、強度と軽量性を兼ね備えた次世代の締結部品です。特に、CVB炭素繊維を用いた製品は、強化繊維と樹脂を最適に組み合わせることで、圧倒的な引張強度を実現しています。これにより、厳しい荷重条件下でも優れた耐久性を発揮し、構造物の安全性向上に寄与します。
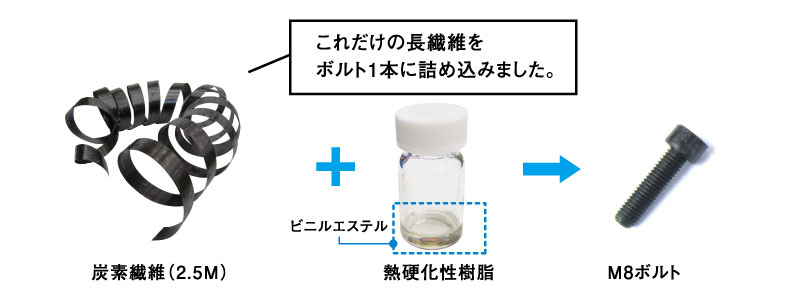
また、炭素繊維の特性として軽量性があり、従来の金属ボルトと比較して重量が大幅に軽減されます。これにより、設計の自由度が高まり、軽量化が求められる航空宇宙や自動車産業においても大きな利点となります。
さらに、炭素繊維ボルトは高い耐薬品性を備えています。腐食性の高い環境でもその性能を維持できるため、化学プラントや海洋構造物など、過酷な環境での使用に適しています。これにより、メンテナンス頻度が低下し、長期的なコスト削減も可能です。炭素繊維ボルトは、これらの特性を最大限に活かし、強さ・軽さ・耐薬品性を追求した製品を提供することで、様々な産業分野のニーズに応えています。
引張荷重試験
炭素繊維ボルト M3x15を使用 501MPa 2520N
炭素繊維ボルト M8x30を使用 342MPa 12500N
(RENYボルト M3x15を使用 151MPa 760N)
(RENYボルト M8x30を使用 164Mpa 6000N)
せん断力
炭素繊維ボルト M8x30を使用 328MPa 12000N
(RENYボルト M8x30を使用 112MPa 12000N)
ユンカー振動試験
炭素繊維ボルト M8x30を使用 残留軸力2.4kN
軽量
プラスティック製と同等の重量にもかかわらず、、強度区分4.6(4T)相当の強度を有する『CBV』。装置の軽量化が可能となり、稼働による電気量の低減・高速運転・運搬の負担の軽減などに貢献。
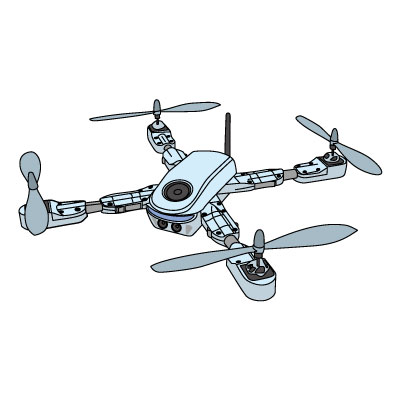
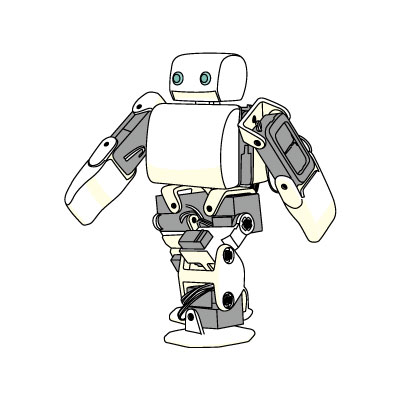
優れた耐薬品性
PEEK製のボルトと同等な耐薬品性を持ち、強度は5倍を達成した『CBV』。ボルトの締結力が上げられるため確実に固定、安全・安心に貢献。さらに、ボルトのサイズダウンが可能となり、装置全体の小型化が可能。
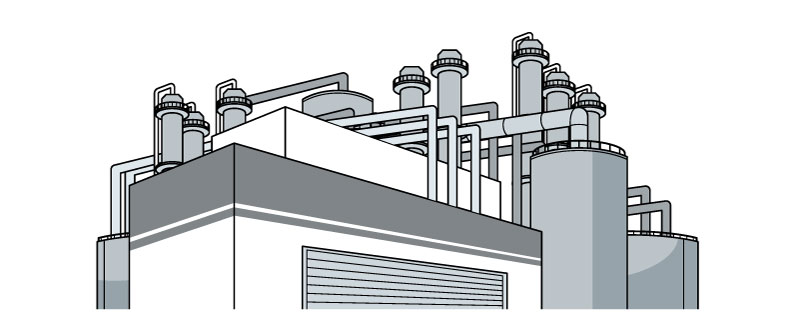
高いX線透過率
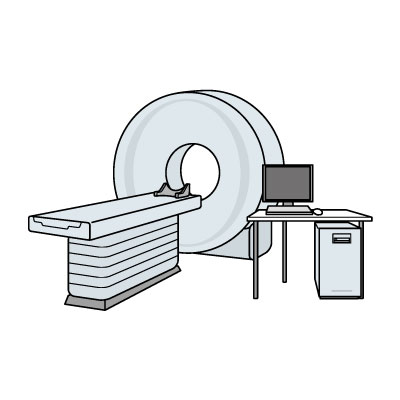
高い透過率を有する炭素繊維を仕様。CTスキャンなどのX線を透過したい用途に使用可能。
非磁性
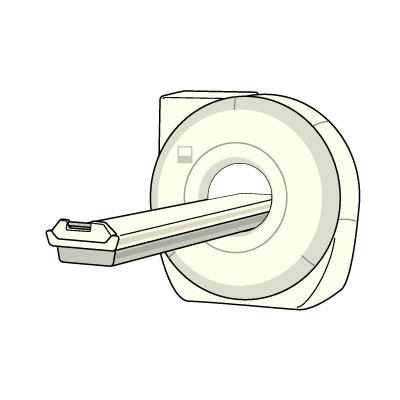
炭素繊維複合材料の非磁性を利用し、MRIやMRI機械室などの用途にも使用可能。